Ouvry specialises in the design and manufacture of protective clothing nuclear, radiological, biological, chemical and explosive (NRBCe) threats. One of the key factors in the performance of personal protective equipment (PPE) is the efficiency with which hazardous agents are filtered, and more specifically the choice of active carbon used. This material plays a crucial role in the suit’s ability to block or neutralise toxic substances, particularly chemical and biological warfare agents. Among various forms of activated carbon, Ouvry has opted for the use of carbon microbeads, a solution that offers numerous technical, strategic and economic advantages.
Why choose carbon microbeads?
To answer this question, it is first necessary to recall the characteristics of the three main families of activated carbons.
Activated carbon is a material whose physical and chemical properties are used to adsorb (trap) toxic molecules, such as gases and chemical vapours. In field of CBRNe protection, activated carbon is an essential component filtration. There are four main families of activated carbons used in protective equipment:
Granular carbons are commonly used in industrial applications, in particular to air or water. Their granular structure provides relatively large adsorption surface area. However, in highly demanding applications such as PPE, this form of carbon can lack robustness and long-term effectiveness.
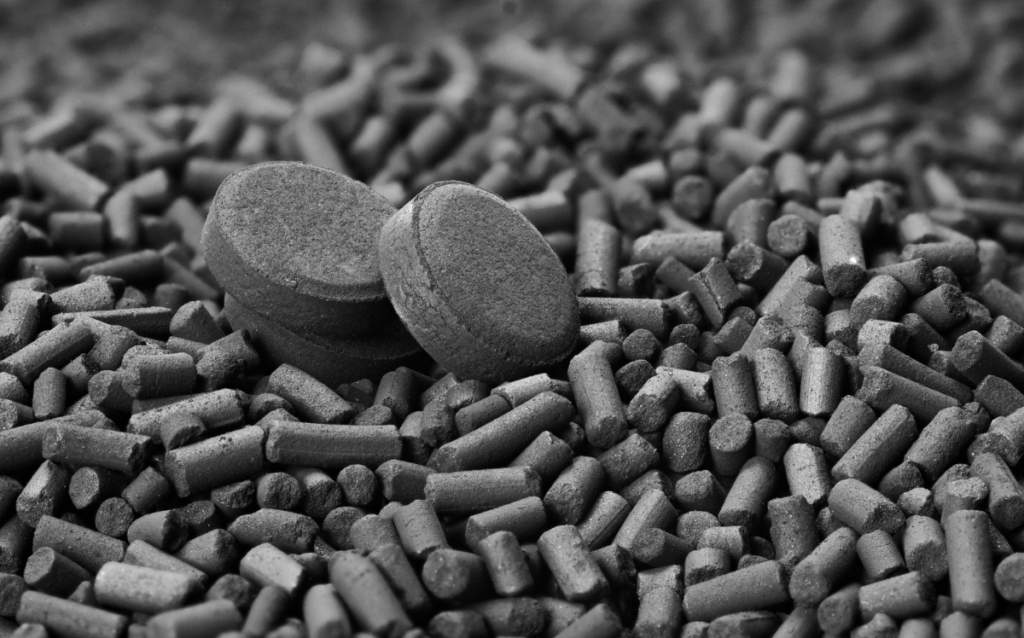
This type of carbon is often prized for its large adsorption surface area, which makes it particularly effective for filtering chemical agents. Coconut-based carbons are widely used filtration applications for their ability to adsorb a wide range molecules. However, they have limitations linked to their geographical origin, mainly in Asia, and their vulnerability in terms of robustness and washability in intense use environments, such as in PPE.
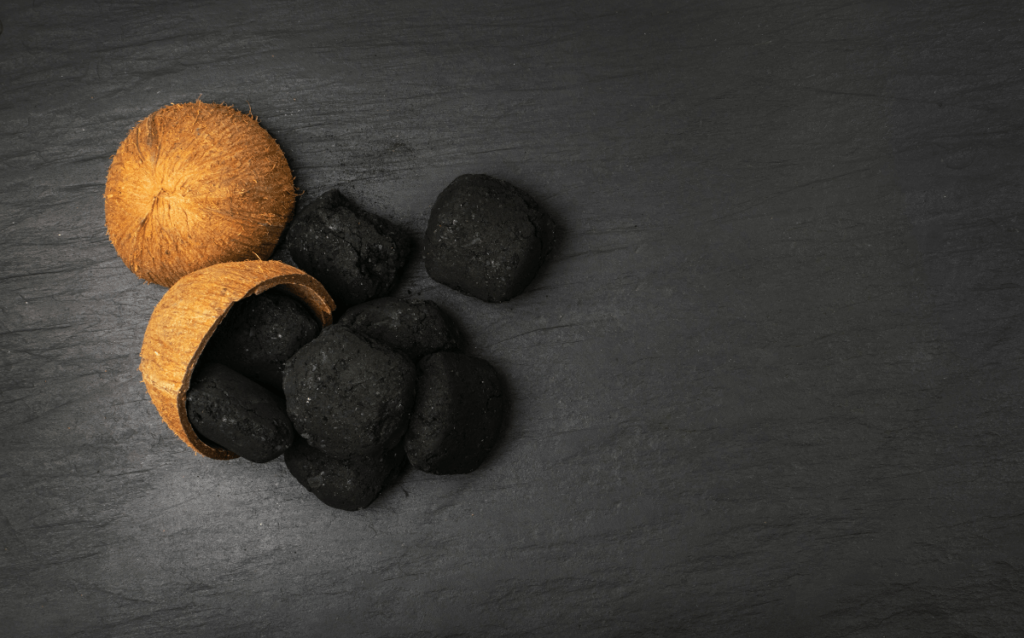
Synthetic carbons are designed specifically to meet particular filtration needs. Their structure maximises efficiency while retaining a certain lightness. This type of carbon is often used in single-use products, but has weaknesses in terms of durability and the ability to be washed without losing its filtration properties.
There is a final technology, Activated Carbon Fabrics (ACF), which dates back to the 1960s. ACF technology is the result of carbonising and then activating precursor fabrics. This technology, which is of interest in the field of filtration, has limited mechanical properties, which make it unfit for CBRN combat clothing.
In this context, carbon microbeads, a type of synthetic carbon, represent a promising alternative, combining efficiency, robustness and durability, while meeting strategic manufacturing and supply criteria.
Technical reasons for choosing Carbon Microbeads
Carbon microbeads are specially designed to maximise adsorption surface area while maintaining a compact, lightweight structure. These characteristics optimise the filtration capacity of chemical and biological agents, which are major threats in high-intensity situations. Compared with granular or carbons, carbon microbeads have a greater exchange surface and are therefore more effective at capturing molecules of various sizes and improving the duration of PPE protection.
What’s more, the uniform distribution of the microbeads throughout the fabric of the protective clothing ensures even filtration and reduces the risk toxic agents seeping in. This precision in the manufacture and distribution of activated carbon improves the reliability of protection, even under extreme conditions.
Carbon microbeads offer increased resistance to mechanical stress, high temperatures and friction. Because of their small size and uniform structure, they are less likely to disintegrate or deteriorate over time, even after repeated washing and exposure to field conditions.
This durability is essential for equipment such as CBRN protective suits, which need to be cleaned after each use without compromising their performance. Carbon microbeads enable optimum protection to be maintained even after several washing cycles, which remains a technological challenge for other types of activated carbon, such as granular or coconut-based carbons.
The ability of PPE to be washed and reused is a fundamental criterion in the choice of materials. Thanks to their homogeneous, stable structure, carbon microbeads do not lose their filtration properties even after prolonged use. This means that users can enjoy high-quality protection over the long term, without having to replace their equipment frequently, which represents a major economic advantage.
Strategic Criteria: Independence and Production Capacity in Europe
Another key factor in the choice of carbon microbeads is the strategic independence they give Ouvry. In fact, carbon microbeads are manufactured in Europe, which guarantees a secure, local supply should the need arise. This independence from imports from Asia (particularly for coconut-based carbons) is essential, especially in times of geopolitical tension or high-intensity conflict, when supply chains can be disrupted.
Ouvry has invested in production capacity located in Europe. This strategic location of production units guarantees responsiveness and flexibility adapting to the urgent needs of armed forces and emergency units. In the event of a rapid increase in protective equipment requirements, Ouvry is able to supply CBRN protective suits in large quantities, while maintaining strict control over the quality of the materials used.
In comparison, other types of activated carbon, such as activated carbon, are often produced in remote regions, which can lead to long delivery times and increased dependence on countries outside Europe.
Conclusion
By choosing carbon microbeads for its CBRN protective clothing, Ouvry is meeting major technical and strategic challenges. The effectiveness of these microbeads in providing optimum protection against chemical and biological threats, their robustness allowing easy maintenance and their manufacture in Europe guaranteeing strategic independence, make this choice an essential asset for the company. This choice contributes to reinforcing the safety and resilience of protective equipment in high-risk environments, while ensuring Ouvry maximum responsiveness to constantly changing needs, particularly in times of crisis.